Computational Fabrication
Piotr Didyk
Computational Fabrication
In recent years, there has been a tremendous development of new, three-dimensional (3D) printing technologies. While 3D printers are still not as popular as regular 2D printers, this may change very soon due the great possibilities that they offer. Instead of using traditional manufacturing techniques, such as cutting or injection molding, 3D printers can create complex three-dimensional objects by disposing small portions of printing material and building objects layer by layer. Besides the fine control over the created geometry, new 3D printers can use multiple materials that can be placed almost arbitrary within the printing volume. This enables not only a fine control over the final appearance of the printed objects [ figure 1 ] , but also over their mechanical properties [ figure 2 ].
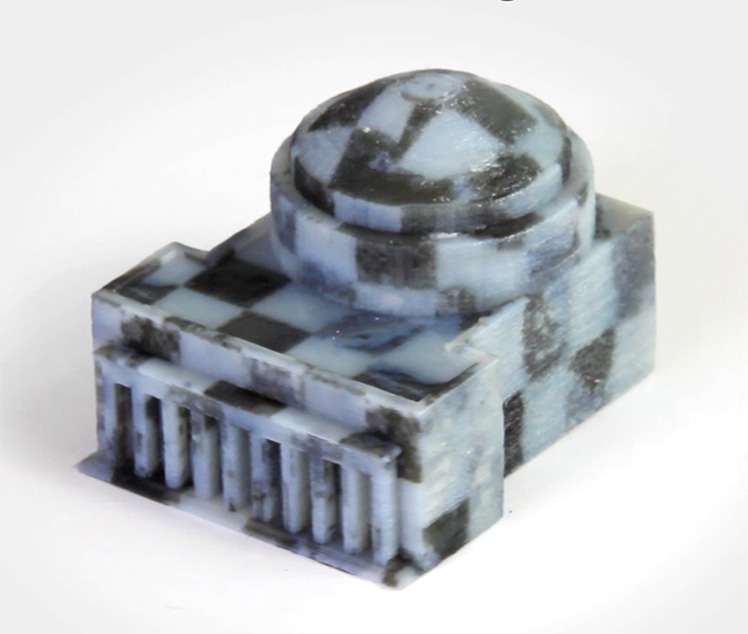
Figure 1: 3D printed model of a building with prescribed texture and subsurface scattering properties.
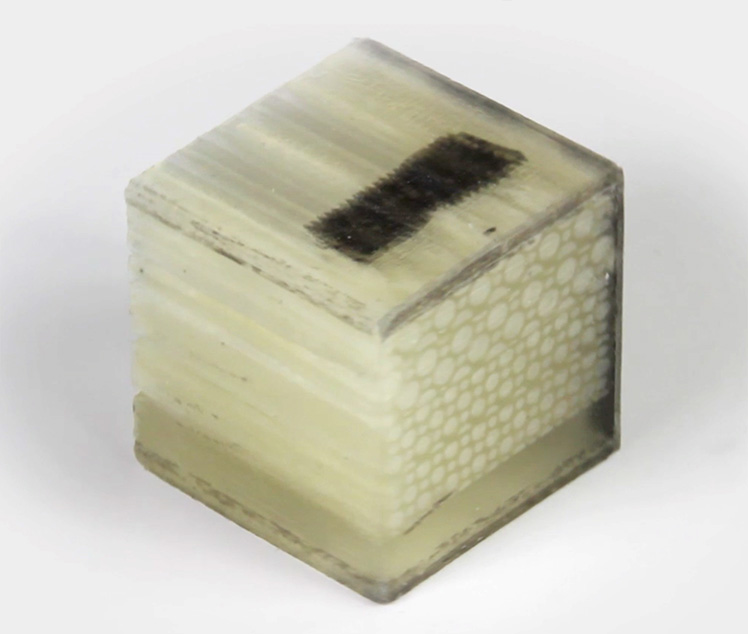
Figure 2: 3D printed model of a book with prescribed deformation properties.
While the fine control over the material placement provides a great flexibility in terms of what can be manufactured, it also poses some computational challenges. Given an object with specified properties (e.g., mechanical or visual), it is unclear how to combine materials available on the printer to achieve best results. Solving this problem requires optimizing for a material placement, which provides properties as close as possible to those that were specified. Due to a number of limitations of current 3D printers such as limited printing resolution, color reproduction, or material properties, there is no guarantee that such a process will succeed. This makes producing hardcopies of real objects still very challenging. In our work, we argue that this problem can be, to some extent, overcome by accounting for human perception. We believe that good understanding with regards to how the printed objects influence user experience is necessary to fully utilize this kind of technology.
An example of such a perception-driven fabrication approach is our recent work on compliance, which addresses the problem of printing deformable materials. Given a deformation property of an object that we want to print and a limited number of different materials that are available on the printer, we want to choose a material that best matches our goal. Answering this question requires building a computational model that can predict perceived differences between different materials. To this end, we first conducted a number of experiments to investigate the ability of human observers to discriminate differences between materials of varying softness. Then, based on these experiments, we built a computational model that can quantify those differences. Such models can be used later to compare perceived properties of different materials and choose the one best suited for printing the desired object. We believe that building similar models for other properties of printed objects will enable us to produce objects that are not only close replicas in a numerical sense, but also perceptual.

Piotr Didyk
DEPT. 4 Computer Graphics
Phone +49 681 9325-1009
Email pdidyk@mmci.uni-saarland.de